The week long intensive course at the
Corning Museum of Glass as an Introduction to Venetian Techniques with William Gudenrath is perhaps the best start on a journey to improving the skills of working with hot glass. Even if one does not want to become a Goblet Master (that would be a great reality television series on Spike, Dave Navarro - "Who will be the next Goblet Master?") this class will impart a level of learning that is unparalleled.
It is a difficult class requiring a lot of work. The hours are long, usually starting the day at 8:00 a.m. and going until 11:00 p.m., there is a lunch and dinner break but always something to do during those hours too. The skill building is repetitious. The techniques are brand new, so push aside everything you know in order to be open to learning these new orders of operations. There is a formula to follow to make these very specific items and if that formula is followed, great success is a result. I believe it is important to have a foundation in the basic skills of glassblowing, the structure of this class helps to build and reinforce those basic skills.
The teaching style of Mr. Gudenrath, Bill, is really very good. He describes the process, shows the steps involved several times, students practice the process. Then he demonstrates again and students practice some more. He introduces new techniques and then revisits the earlier teachings. This results in building confidence and skill in the students. Bill is the Sage on the Stage, a true master of the art. He is also a wonderful Guide on the Side ensuring students are on track. Be sure to check out his ebook on the
Techniques of Renaissance Venetian Glassworking (
http://renvenetian.cmog.org/) The videos posted are simply fantastic, great care and detail has been spent showing step by step processes on the creation of a large variety of objects.
Coating Gather and Collecting Gather:
Students first create the caterpillar and in order to do so they must first learn how to gather the glass on the punty rod. Gathering with a covering gather and then a collecting gather. The covering gather is designed to get a base coat of glass on the rod. Turning in the glass to gather is key to any glassblowing. The ability to get a consistent and controlled amount of glass is a fundamental skill. There is the breaking of the surface of the glass, a push forward to about an inch depth on the rod, turn turn turn, and then a very fast turn as the rod is lifted out of the glass (a slight push forward here) and the glass spools onto the tip of the gathering rod. Once the glass is gathered cool the pipe to allow for greater control and pressure when approaching the marver table.
The Pipe Cooler:
I do not think I really understood why to cool the pipe until around Thursday of class. The pipe is certainly hot and I have trained myself where to grab the pipe to allow good pressure on the marver table. By cooling the pipe it allows the pipe to be grasped and pushed fairly close to the head. This really effects the shaping of the glass on the marver and gives greater control over the shape.
The Caterpillar:
However, for the caterpillar go right to the bench. The very tip of the glass is pinched slightly with an outer motion with the pincers or tweezers about three times. Then move the pincers to the side and pull the glass outward with a firm motion stretching the glass into a tube shape. Using the jacks create several constrictions in the glass forming the rings (the body sections) of the caterpillar. Pull again slightly to straighten the piece. Set the head on the rail and push inward with the tips of the pincers to create the eyes and the back end to create a smile. Midway in the body turn and lift with the pincers with a blade on top and one on bottom creating the inchworm look. Pull the head back in line with the rod.
The Merese:
Later in the day students practiced the
Merese. With a coating gather students make a post on the end of punty rod. This is just a fairly thick gather marvered on the rail of the bench using the back end of the jacks to flatten the face of the glass. The assistant brings over a fresh collecting gather of glass and their punty rod is grabbed with the pincers. While turning the fresh glass is pressed onto the rod. Turn the rod and track the hot glass to the side. this collects the glass on the tip of the rod. Cast downward to cut the stream of glass. With the back of the jacks push push push gently flattening the fresh glass. Then angle the jacks forming about a 10 degree angle on the glass. Jack the line between the rod and the fresh glass then place the blades on either side of the merese and cap the shape. To me it looks like the profile of an old cardinals hat or maybe an oriental rice hat.
Pretty good video.
We worked on the post and merese any time there was a break in the action. If a bench finished ahead of the others our instructions were to work on the merese. That practice of this fundamental step leads me to believe it is more important than it lets on.
I created a blog entry using fimo clay to simulate the merese.
http://gafferslog.blogspot.com/2017/06/the-merese.html
The Punty:
The Punty is a term used for the gathering rod. It is also the term for the attachment in making a transfer of the piece from one pipe or rod to another rod. I have heard Pontil means bridge. Do a coating gather on a rod then marver the glass gently and quickly. Grab the tip of the glass with the pincers and pinch, pull outward and then down and inward to strip most of the glass off the tip of rod leaving behind just a small moon of glass. This rod then goes in the pipe rack next to the glory hole.
Slide the punty into the glory hole behind the door, about two moves before the transfer giving it plenty of time to get red hot. It is shaped on the right rail of the bench using the side of the pincers to flatten the top leaving a bit of a moon maybe around 3-4 mm thick from the end of the rod. Lift to blow fiercely on the tip of the punty and attach it to the center of the piece. Using the pincers push and lift as necessary to help center the punty. I like to have one blade of the pincers on either side of the pipe and tweak them hard against the pipe to push the punty into place.
Be aware in this process the piece is "cold" and the punty is hot.
The Standard Setup:
The Standard Setup is the basic shape of all the blown pieces. It consists of four basic steps to shape the glass. Begin with a collecting gather, if not enough glass can be gathered on the first gather of glass then do a coating gather followed by the collecting gather about 5 to 7 seconds later. Remember the coating gather is small and allows the glass to strip off the pipe a bit. The cooling of the surface allows for a good second gather while maintaining a hot core of glass from the first gather.
The pipe is placed on the pipe cooler helping to chill the pipe making for easier handling of the pipe closer to the glass. This is essential to get a firm pressure on the pipe and greater control over the glass. Touch down at an angle on the marver. Lift up to parallel on the marver and give firm downward pressure. This will squeeze the glass out into a tube shape. Be sure not to over marver as the glass needs a deep heat for the blow. Lift to blow for about three seconds straight to push the plug out of the pipe. Be sure the glass is centered (may require a quick marver) and then cap and blow the pipe. Keep the pipe parallel at this time. Release the pressure with the bubble is about two thirds to three quarters of the size of the gather. Rotate the handle end up and marver the tip of the glass. Be sure to have a light touch down. The glass should even stretch a bit and certainly should not be pushed into the pipe (which is typically what I will do when marvering).
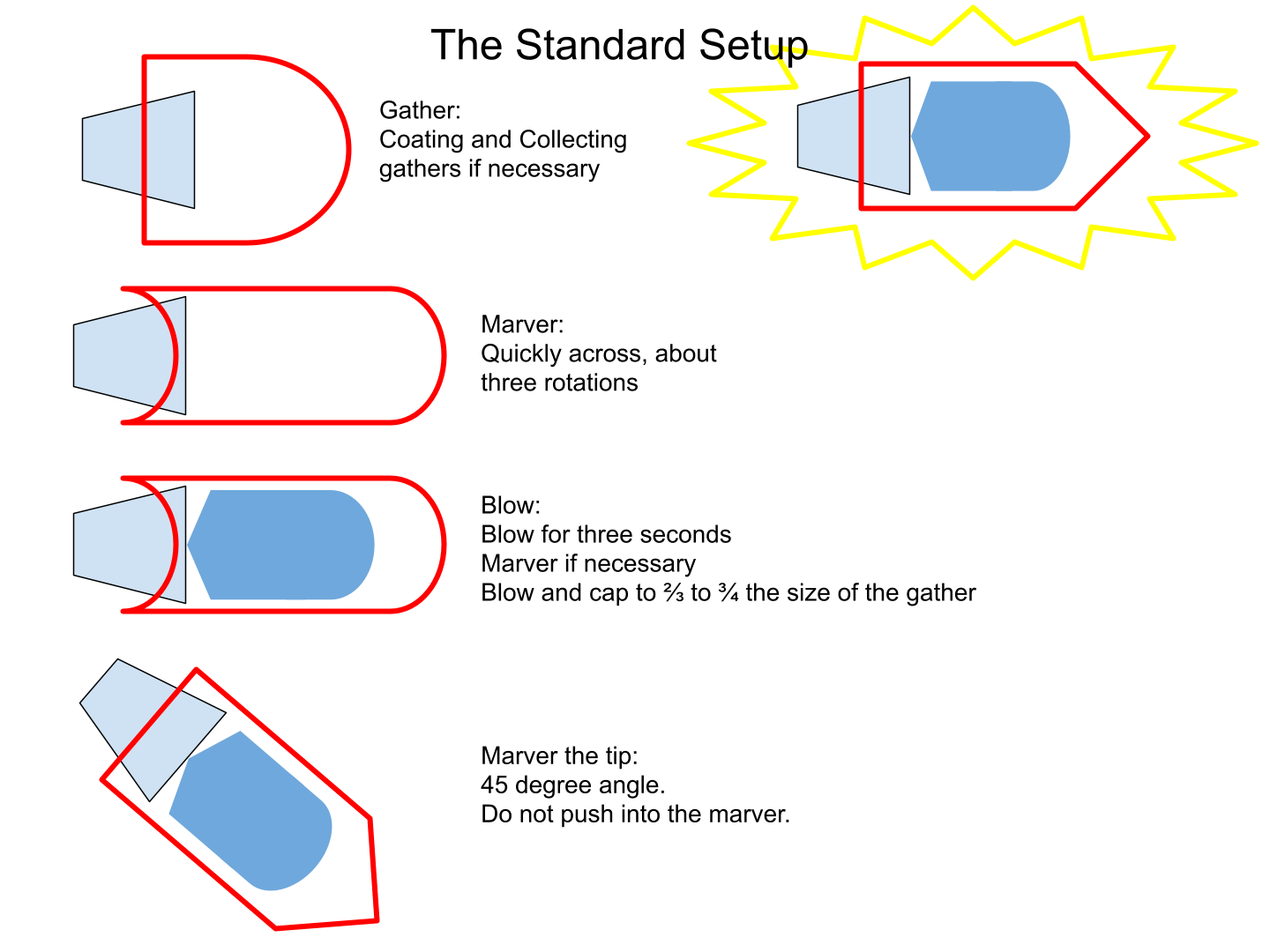
The Necked Sphere Method:
- Begin with the standard setup (detailed above)
- Reheat Behind the Door
- Marver the tip of the piece on the right arm rail of the bench. (Be sure not to press but let the glass stretch just a bit, just as we did on the marver.) Blow up the piece to 50% of its final size, start the neck (this is about half way of a neck line to maintain the stability necessary during the next heat.
- Reheat - Behind the Door
- Blow up to 100%, complete the neck and shoulder of the piece (be aware of the shoulder shape and the taper required. Think about the thermal shock associated with the shape of the shoulder)
- Heat the bottom, (It is at this stage to begin stretching the piece takes place, hand the piece down or swing it after heating the bottom third to half of the piece) touch the sides to create a cylinder, heat bottom and flatten the bottom
- Cool the punty site, flash and transfer
Opening process
- Heat the end and open to 1" diameter (be sure to heat close to the door)
- Heat deeper and soffietta
- Heat shallow, open more, immediately soffietta
- Reheat shallow and final opening
- Heat treatment for final shape
Behind the Door:
A few words on Behind the Door... Heat. Radiant heat. Deep heat. When entering the glory hole it is important to heat behind the door. The best heat comes from that position. Heat reflects off the surface of the door bouncing back onto the piece giving additional and vital heat to the piece or to the punty. Get in the habit of it.
The Heat Treatment:
The Heat Treatment is key in getting a good final shape or making adjustments to the piece. After the final opening go in for a deep heat behind the door. This is a five second heat, turning the rod as slowly as possible. Come out for one second. Go back in for five and out for one, then go back in for five. Head to the bench for the final shape with the jacks on the outside of the piece. You know that little waist the glass can get? This will remove that waste. Watch your pressure downward with the jacks. I pushed too hard once and the piece jumped off the punty.
The Neck and Shoulder:
The constriction on the neck is important in having a good break off the blowpipe. It is smooth and deep. Seemingly it is about an inch away from the end of the pipe. The shoulder shape is important to avoid the thermal shock. When creating the shoulder lean out with the jacks at about a 45 degree angle. "Massage" the neck and shoulders with the jacks. Do not simply push. Work the line in and out with the jack blades. The taper on the shoulder prevents the thermal shock, as a rounded shoulder with crack when going back into the glory hole after the transfer.
The Blown Foot
The foot consists of a collecting gather. If really necessary do a coating gather first. Do a very quick marver into a cylinder form. Blow for three seconds then straighten the glass, marver quickly if necessary. Then blow and cap the pipe. Ideally the bubble will fill the gather of glass. Watch though the bottom does not get to thin. Hang down on the way over to the bench. Jack the glass just off the pipe end by about an half inch. Then lean hard with the jack blades at a 45 degree angle or better. This moves the glass outward making a long thin neck. Blow gently to inflate the bubble at the base. At this stage it looks like a miniature roman bottle.
Go in for a deep heat behind the door. Turn for a bit building heat but then flip the glass back and forth to watch movement. Let the glass hang down on the pipe as you come out of the glory hole, the pipe is parallel. I would cap the pipe at this stage. Swing up to present the glass.
The gaffer takes the pipe in the shears and guides the glass onto the merese. All the while turning the blowpipe. The assistant blows ever so slightly. The gaffer pushes the bubble down onto the merese covering it to the tip and it really squishes on. Lift upward on the foot pipe, blow softly, remove the blowpipe from the lips to cut the bubble.
Get into the heat quickly. Back at the bench pull a bit on the tail to straighten the foot. Jack a deep line in the glass. Lean at a 45 degree angle both directions. Hold the line with the diamond shears and tap the tail off the foot.
Back into the heat behind the door if possible. Come out to open the end with the jacks to about one inch diameter, quick heat, soffietta, and jack the opening and flair the foot open. Flatten with the blades of the jacks. Do not use a paddle as the glass can not take the thermal shock.
Blow Yank Blow
Blow Yank Blow is another method for making a vessel.
- The Standard Setup, although when marvering the tip is gets extra marvering to really chill that area.
- Reheat Behind the Door, attach the blowhose
- Marver the tip on the right rail, with the diamond shears pull the glass outward about two inches, cradle the end of the glass keeping it centered. Blow, Yank, Blow. Blow very softly at first, then harder and harder (do not over inflate the bubble to quickly, be sure to keep center). The blow makes the glass round, to me it gives the illusion of using the diamond shears to push into the bubble. The yank is a slow firm movement outward, there is pressure on the bubble but not really blowing occurring, this stretches the glass. Blow again to inflate the body, when done correctly the the glass is almost in a cylinder shape. - Jack the neck, be sure to follow a good neck form with the tapered neck, Trim off the tail, to do this jack a spot fairly near the end of the bubble (I would say almost a half moon shape not a crescent moon of solid glass at the tip) and knock off the tip.
- Optional reheat behind the door and complete step three as necessary.
- Gently heat the lower half of the vessel, touch the sides with the jacks to straighten the cylinder, blow gently to elongate the cylinder. This really rounds out the bottom and gets it in line with the sides of the vessel.
- Add a merese or heat and flatten the bottom.
- Transfer and open
Opening process
- Heat the end and open to 1" diameter (be sure to heat close to the door)
- Heat deeper and soffietta
- Heat shallow, open more, immediately soffietta
- Reheat shallow and final opening
- Heat treatment for final shape
Bowls :
The Blow Squish Blow
The follows the blow yank blow method except instead of yanking to lengthen the bubble push inward with the diamond shears squishing the bubble wider and flatter. This technique is used to create a bowl shape.
Necked Sphere
Using the Necked Sphere method once the piece is blown to 100% and is round, heat the bottom like for the stretch except come out and up with the piece. Cap the blowpipe so no air can leave. The bottom of the bowl will begin to flatten. Do this about three times to get a good shape on the bowl. Jacks on the side to shape the wall. Flatten the bottom, transfer and open the bowl.
To open the bowl jack the opening to about 1.5 inches. Heat and then soffietta. Only soffie the bowl one time instead of two like in a glass.
Low Bowl with straight side
Gather, block with number 6 standard block, gather. Do the standard setup
Blow to 50%, Neck, Heat
Blow to 100%, Chill the neck with the jacks
Heat
Come out and angle up with the pipe capped to get the spheroid shape (think m&m)
Jack the neck. Lean outward to shape the neck to avoid thermal shock.
Cool the punty spot, Do not flatten the bottom as this occurs with the parchoffi jacks
Punty to transfer
Heat the lip
Open to about 1.5 inches, Heat a bit deeper, Soffietta
Can fold the lip in or out
Deep heat behind the door
with the parchoffi push down and toward the bench at the inner edge of the bowl.
This will flatten the bottom.
Jack the sides straight.
Thick bottom Glass:
After the standard set up, heat, and head over to the bench. Flatten the bottom of the glass. Then blow. Using the blow hose is best here in adding air and keeping the jacks on the sides and bottom of the glass inflate to size. Transfer and open the piece as normal.
Also can insert the jacks or an ice pick into the bottom to create a hollowed out place. Get a good gather from the furnace and drop it on the bottom of the piece trapping an air bubble in the bottom. Heat to melt in the seam. Blow and shape as necessary.
Rakow Gallery Opening:
On Friday evening there was an opening at the
Rakow Library. There was a fabulous party. I want to thank Amy Schwartz for allowing us to attend the party and opening. What a great experience. One of the highlights of the evening for me was getting to meet Paul Engle. I have been following his blog (
http://www.conciatore.org/) for a couple of years now. I want to thank Paul deeply as he gifted me a copy of his book.
Supplies:
2 inch aluminum puffer:
http://products.steinertindustries.com/2-0-aluminum-puffer/
90 degree swivel:
https://www.abrimagery.com/store/product_info.php/14quot-degree-brass-double-swivel-p-102026?osCsid=713521d653acd3168acd75a779271d17
Resources:
Class Schedule - with everything else going on the days are full. Usually starting at 8:00 a.m. and going until 11:00 p.m.. The charging days on Wednesday and Friday were a welcome break. I think that is a great benefit of classes at Corning with the additional studio time at the end of each class day.
 |
Class Schedule |
Voice Recordings of the steps:
Necked Sphere Method
Merese
Blown Foot Steps
Blow Yank Blow
Board Photos:
 |
Necked Sphere Method |
 |
Proper Neckline and Shoulder |
 |
Bill wrote this on the board three different ways |
 |
Blow - Yank - Blow Method |